Receipt of Sequencing Requirements
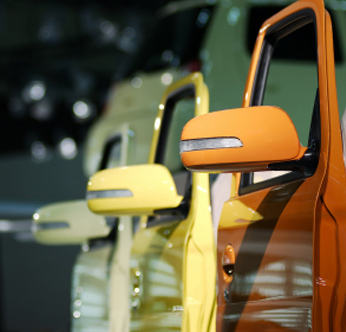
There are various methods and types of communication used by the automobile manufacturers to inform the suppliers of the build sequence. Below are examples of some of them:
A. Electronic Data Interchange (EDI)
- Using traditional EDI, the sequenced requirement usually comes in a form of an 866 transaction (Production Sequence). For example, with Ford, the 866 contains approximately six days of "firm" build information. Other manufacturers, like GM (in some cases) and Nissan, also use EDI transactions to communicate sequencing requirements to their suppliers.
B. Internet
- In some instances, the build information is made available to the suppliers on the Internet. For example, an automobile manufacturer may post the requirements on a secure supplier web site, where the supplier can download it into their system. Sometimes, this becomes the function of the supplier's corporate office, and then they take the responsibility to make this information available to the appropriate plants on their wide area networks, or via FTP to the plants' systems. Saturn does this for their sequencing needs.
C. Broadcast Pulse
- Another common way for suppliers to receive sequencing data is via a broadcast pulse. This is prevalent with plants where the suppliers are located relatively close to the manufacturer, usually no more than an hour's drive away. Usually, the pulse is triggered when the vehicle passes a certain predefined point on the manufacturer's assembly line (such as when the vehicle exits the paint section), and the requirement is broadcast to the suppliers, one vehicle at a time. General Motors' GM Flex broadcast works this way.
The automobile manufacturers usually determine the means of communicating the sequencing requirements on a project-by-project basis, and then communicate that to the suppliers, so they can set up their systems accordingly to be able to receive the data. One of the more common broadcast systems used is General Motor's Flex system, which is standardized with some variations across their North American manufacturing facilities. Sometimes it is via T1 connection directly to the supplier with specific information, and sometimes it is over he internet. Redundant communications are usually built into the communications in case of the primary going down.