Production Options
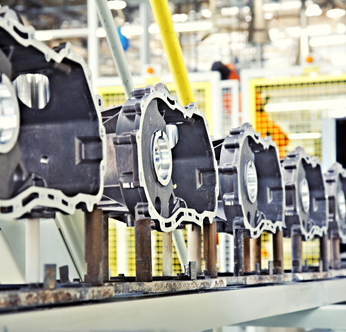
Once the suppliers know the requirements, there are several different options to manufacture and deliver the parts in sequence to the manufacturer. These mostly depend on the nature of the product, how the products get packaged, and other factors considered by the suppliers.
Sometimes, the parts are built in batch (bulk), and are only sequenced at the end of the manufacturing process by placing the parts in proper sequence in the shipping rack, and then loading the shipping containers onto trucks in the proper sequence. Another option is that they continue doing business as usual, and outsource the sequencing aspect of the project to a third party sequencer. Yet another option is to build in sequence. The following section describes these options in more detail.
A. Build in Sequence
- In this environment, the supplier receives the sequencing requirements and builds the parts in that order to match the sequence order as communicated by the manufacturer in one of the above listed Receipt of Sequencing Requirements. There are different variations of building in sequence. Attributes to consider include the nature of the product and how the product is packed at the end of the line as well as how the shipping racks are loaded on the truck. Some suppliers have a need to reverse the build sequence of a certain number of parts in order to accommodate packing requirements. This may be necessary in order to ensure FIFO principles, despite the design of a shipping rack, which may only allow for the last part placed in it to be pulled first by the manufacturer. Reversing the build sequence can help ensure the use of FIFO. Still others need to reverse build entire trucks due to lack of floor space for storage.
- One of the major benefits for a supplier to build in sequence is to maximize the utilization of the supplier's floor space, because there is no need to store more than a minimal amount of finished goods.
- One of the possible drawbacks to building in sequence is the business issue associated with falling behind in production requirements in the event of a major disruption on the supplier's assembly line, such as a machine breakdown. If enough time is not allotted into the buffer time and a failure occurs or the supplier is unable to address the issue within a specific timeframe, the timely delivery of parts to the manufacturer may be compromised. It is critical, on the part of the supplier, to plan for adequate contingencies, in such instances.
- Another consideration on the part of the supplier is to ensure the integrity of the build process, and that the finished good is built using the correct substrate, if applicable. Even though such faulty production may likely be caught at the time of the verification of the proper part being built from the proper substrate and placed in the proper slot in the rack, the supplier may have added value to the wrong part that now may be in need of rework or even scrap.
B. Build in Batch and Pack in Sequence
- This method is often adopted by suppliers due to its simplicity to implement. Conceptually, the process mirrors what they are doing already, with the exception of the change in the way the products are placed in the rack and shipped. A drawback to this method is that it generally requires more floor space to be set aside for warehousing of finished goods. In most cases, the floor space is the biggest concern for this method.
- As with any process, this method can be automated in ways like; pick to light assistance, conveyor lines driven by requirements, Radio Frequency (RF) directed picking as some examples.
- Another drawback to this method is that the supplier must keep close track of the inventory levels, especially when engineering changes occur.
C. Third Party Sequencer
- This option is generally selected by suppliers that have minimal resources available or have no desire to implement and support the systems necessary to facilitate sequencing in house. In turn, they outsource that part of the business to another company whose objectives are to specifically handle these types of business requirements. These third party sequencing companies receive the products in batch from the supplier. They then pick and pack or asemble them to sequence. Finally they ship them in sequence to the manufacturer.
If the third party sequencer is reliable and experienced, partnerships like this may work out well. Both parties do what they are best at, and the manufacturer gets the product exactly as expected. However, if the synergies don't occur, the relationship could become strained and the customer could become negatively impacted. Another consideration with this scenario is that the manufacturer typically pays for shipping costs only once. Thus, any shipping costs between the supplier and the third party sequencer need to be taken into account when the supplier initially costs out the project.