Our methodology
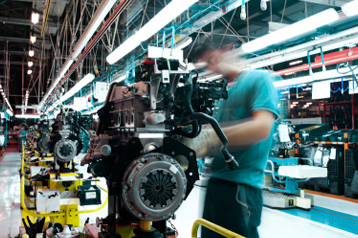
Introduction
The concept of automotive sequencing originated from the just-in-time initiatives introduced by the automotive manufacturers and their suppliers in the early 1990's.
According to AMR Research, automakers are accelerating the sequence requirements. By 2010, more than 70% of a vehicle's content will be sequenced; it is 40% today. Those companies that cannot respond will likely be removed as preferred suppliers.
Learn MoreExplore the following topics:
- Receipt of sequenced data from OEM
- 866 EDI or broadcast pulse
- Pick-and-Pack sequencing
- Build-to-Sequence process
- Sequencing labeling requirements
- Trailer loading in sequence
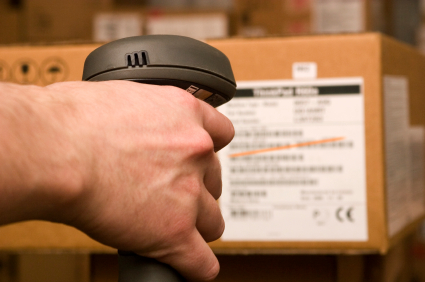
- The essence of automotive sequencing is for suppliers to deliver parts to the manufacturers just in time, and also in the proper build sequence, as requested by the customers. Generally, sequencing maximizes manufacturer's floor space, decreases the time a consumer waits for their new vehicle, and reduces the inventory levels being carried by manufacturer and supplier. Sequencing covers a number of components including doors, quarter panels, overhead systems, seats, wheels, glass, bumpers, exhaust systems,axles, and even engines. Sequencing optimizes production efficiency while also reducing waste and parts storage space.
- The focus is to look at the issues related to automotive sequencing from the supplier's perspective. Furthermore, the information contained herein focuses on this topic from the information systems perspective, and will not elaborate on the physical planning, facilities layout, building infrastructure and other non-systems related areas.
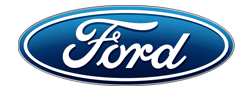
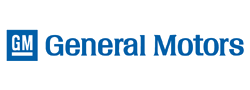
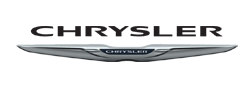
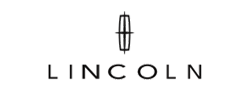
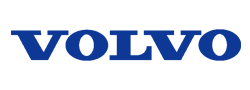
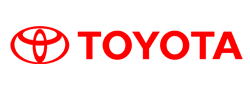
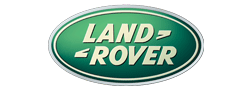
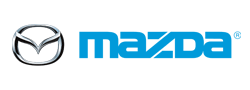
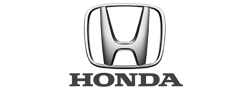
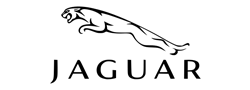